Installing a submersible well pump is more than just a mechanical task; it’s an intricate balance of precise engineering, environmental understanding, and skillful execution. My extensive experience in the field has uncovered numerous insights that regular manuals may overlook, providing guidance for safe and effective installation, optimizing the pump's lifespan, and ensuring reliable water delivery.
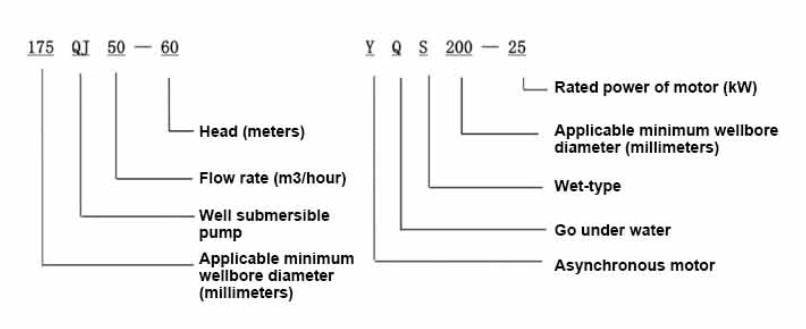
Submersible well pumps are a sophisticated solution to access groundwater efficiently. Unlike surface pumps, submersible pumps operate underground, submerged in water, which offers several advantages including eliminating pump cavitation and energy efficiency due to gravity assistance in the water uptake. However, the installation process is critical; even minor oversights can lead to significant long-term issues.
Preparation begins long before the pump makes contact with the water. First, thorough inspection and evaluation of the well environment are necessary. Conducting a pump test provides data on the well’s yield and drawdown characteristics, vital for selecting a pump with appropriate horsepower and capacity. Over-sizing or under-sizing the pump can lead to undesirable energy consumption and suboptimal performance, eventually causing premature failure.
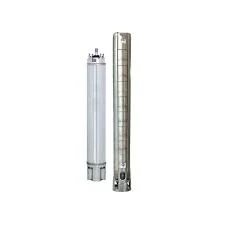
Secondly, it is essential to choose the right materials. Quality piping and cabling are crucial, as they must withstand the rigors of water wear and electrical load. Stainless steel and high-grade thermoplastics are often recommended due to their longevity and resistance to corrosion. Additionally, the electrical wire gauge must match the specifications necessary for efficient power delivery without causing overheating.
Implementation of the pump involves carefully lowering it into the well, ensuring it is securely attached to the drop pipe, and safeguarding it against potential issues like sand infiltration or water turbulence that might raise debris. A significant aspect often underemphasized is the pump’s position in relation to the well’s bottom. Installing too close can increase sediment intake, while too high can affect water intake efficiency.
installing submersible well pump
Wiring the pump requires adherence to electrical codes and standards for safety and efficiency. All connections should be waterproof to prevent current leaks, which might lead to malfunction or pose safety risks. Using heat-shrinkable waterproof connectors is advisable as they provide superior resistance to environmental conditions.
Once installed, commissioning the system must be done gradually. Initial system checks should include measuring the current draw with an amp meter to ensure it matches the motor's rated specifications, an efficient way to diagnose any immediate electrical issues. Monitoring the well's recovery rate post-installation can help ensure the pump is not over-extracting, which could harm the aquifer and the pump itself.
Lastly, maintaining the pump ensures longevity and sustained performance. Regular inspections for electrical anomalies, flow rates, and pressure drops should become routine. Over time, mineral deposits or biofouling can impact pump efficiency, necessitating periodic cleaning. Annual or bi-annual professional evaluations are essential to preemptively address wear and tear or adapt to changes in water quality or supply needs.
In conclusion, installing a submersible well pump transcends a simple plug-and-play affair—it demands precise planning, meticulous execution, and ongoing maintenance. Each step, from preliminary assessment to post-installation care, plays a pivotal role in ensuring optimal functionality and reliability, affirming why expertise and experience are invaluable in the installation process. Central to this is the understanding of the delicate interplay between mechanical design, environmental compatibility, and technical precision. These insights, drawn from extensive fieldwork, provide a framework for a successful submersible pump installation that enhances both the efficiency and reliability of water supply systems.