Understanding the wiring of a 3 phase submersible pump is essential for professionals looking to ensure reliability, safety, and efficiency in fluid management systems. These pumps are commonly used in applications such as irrigation, sewage treatment, and industrial water processes, where understanding the nuances of electrical connections can significantly impact performance and longevity.
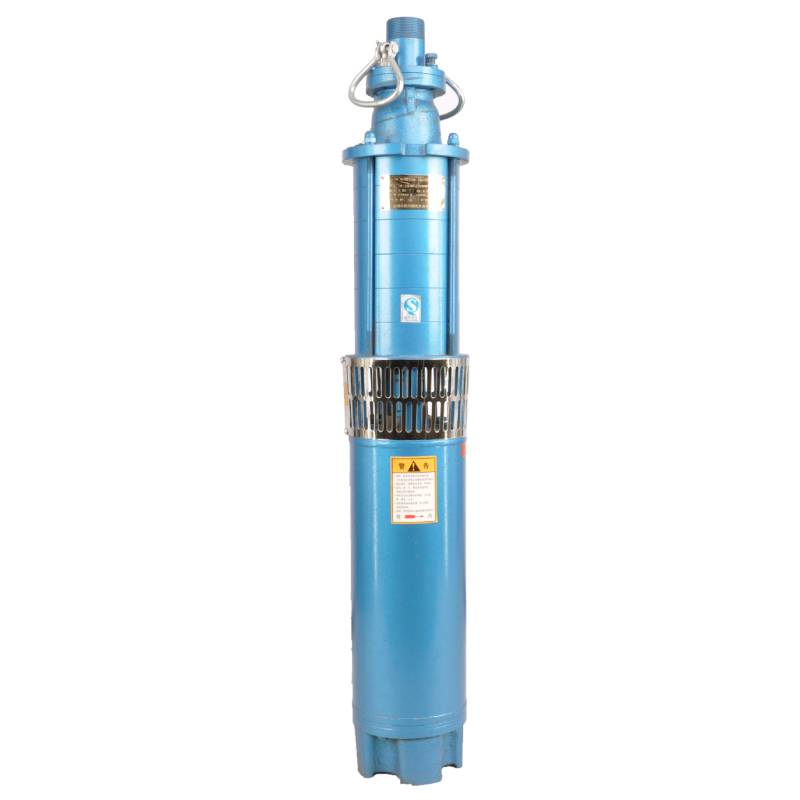
To start,
it is crucial to understand the basic components of a 3 phase submersible pump system. Typically, this includes the motor, pump body, control panel, and the power supply. The three-phase electrical power system, often referenced in industrial settings, uses three wires to carry current and one neutral wire. These wires are labeled as L1, L2, and L3, each carrying a current that reaches its peak at different times, ensuring a consistent power flow and more efficient motor operation.
For installing a 3 phase submersible pump, the first step often involves setting up the control panel, which acts as the brain of the operation. It regulates the voltage and current supplied to the pump, switch operations, and provides necessary protections. A fundamental aspect to remember is using appropriately rated circuit breakers and overload protection devices to prevent damage due to unexpected electrical surges or operational failures.
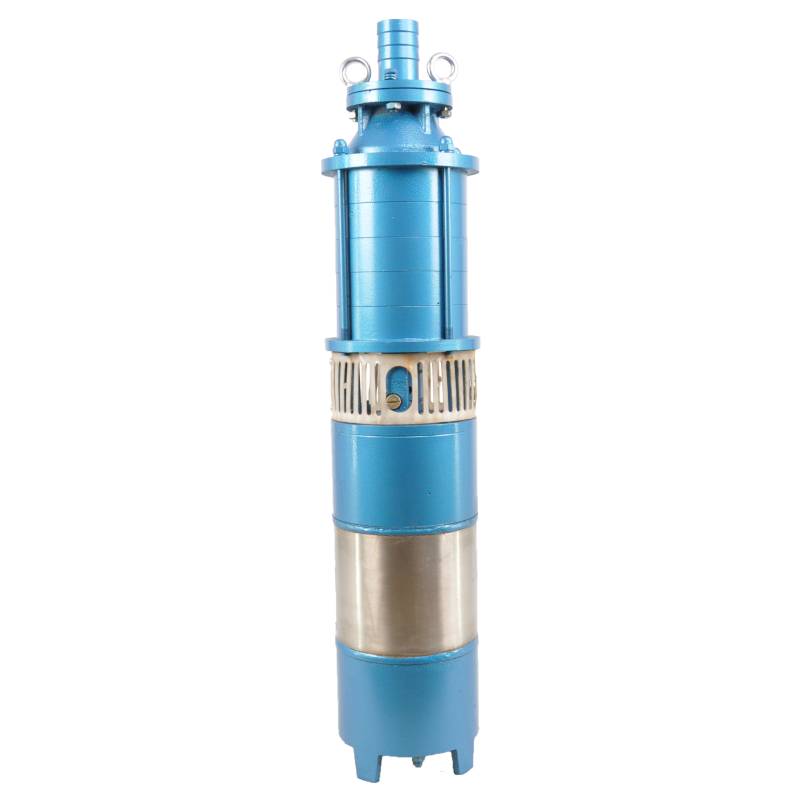
When it comes to wiring the submersible pump, color coding of wires based on regional standards (such as NEC in the United States or IEC internationally) is vital for safety and maintenance. Typically, for a 3-phase system, the colors might be black for L1, red for L2, and blue for L3, complemented by a green or green/yellow striped wire for grounding. The grounding wire is critical for safety, as it prevents electrical shock and equipment damage by redirecting stray currents safely into the earth.
Connecting the wires requires precision and awareness of the rotational direction of the pump. Incorrect wiring can lead to reverse rotation, drastically reducing pump efficiency or potentially causing mechanical failure. Therefore, after completing the wiring, it is advisable to perform a no-load test run. By briefly powering the system, one can observe the rotational direction and make necessary adjustments. If the pump runs in reverse, swapping any two of the live phases (e.g., L1 with L2) will alter the rotation direction to correct this.
3 phase submersible pump wiring diagram
It is also important to consider the specific environmental conditions in which the pump operates. Factors like water acidity, temperature, and the presence of solids can influence both wiring insulation and the choice of material for connectors and junction boxes. Opting for high-quality, corrosion-resistant materials can extend the life of the installation and reduce maintenance frequency.
From an authoritative standpoint, consulting the pump manufacturer's technical datasheet and adhering to local electrical codes provides a framework for best practices in wiring. Technical support and resources are often available from manufacturers for complex installations requiring specialized configurations.
Finally, regular maintenance and inspection form a crucial part of ensuring the system’s trustworthiness and efficient performance over time. Scheduled checks help identify early signs of wear or compliance issues, such as integrity of insulation and secure connections, thereby preempting potential failures.
This framework not only optimizes the functionality of a 3-phase submersible pump but also enhances operational safety and minimizes costly downtime. In-depth understanding and meticulous implementation of wiring guidelines contribute to sustainable operations and are a testament to the expertise and reliability expected in professional electrical and mechanical installations.