Understanding and implementing the correct connection diagram for submersible pumps is essential to ensure efficient operation and longevity of the pump system. Submersible pumps, integral to many industries, are used extensively in applications ranging from water extraction and sewage pumping to oil rig operations and field irrigation. Their ability to function while fully submerged makes them indispensable in challenging environments. When discussing submersible pump connection diagrams, several key factors must be considered, including wiring accuracy, electrical safety, and system compatibility.
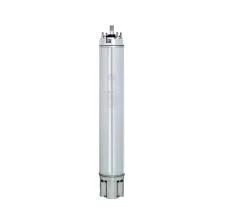
Firstly, it is crucial to grasp the core components involved in submersible pump systems. These typically include the pump itself, the motor, control panel, power cable, and often a discharge pipe.
The reliable operation of these pumps heavily depends on the precise interconnection of these components. Wiring discrepancies or incorrect installations can lead to pump failure or even pose significant safety hazards.
A standard submersible pump connection diagram begins with the power source. This source typically involves a direct connection to the electrical grid or a generator setup in remote locations. The power voltage should align with the pump's requirements, typically stated in the pump's technical manual. It’s pivotal to ensure that the electrical supply matches the pump’s needs to avoid overloading the motor which could lead to overheating and eventual burnout.
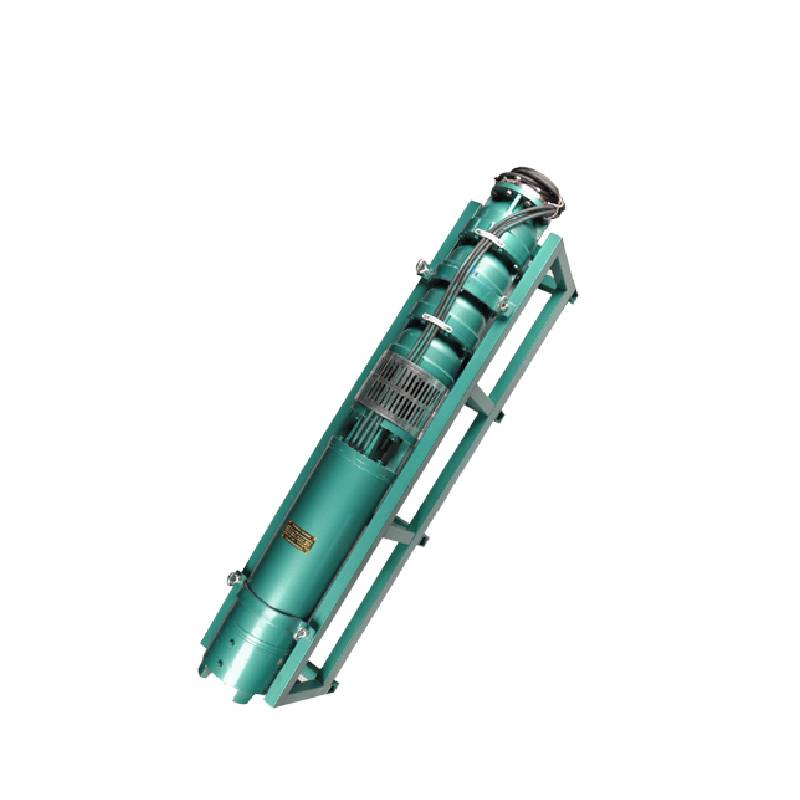
Next in line is the control panel, which acts as the brain of the operation. This panel regulates the pump’s operations, providing essential feedback and controls such as on/off switches, pressure settings, and failure alarms. In situations where the pump is part of a more integrated system, the control panel may also facilitate remote monitoring and automation. Wiring from the control panel to the pump must follow precise guidelines, often provided by the pump manufacturer, to ensure that signals and power are effectively and safely transmitted.
The power cable that connects the pump to its electrical source must be selected based on both the depth of the submersible installation and the electrical load requirements. Given that these pumps operate in submerged conditions, the cables must be waterproof and designed to withstand long-term exposure to wet conditions. Specialists recommend using cables with high-quality insulation and specific protective coatings that can resist deterioration caused by minerals, chemicals, or biological elements commonly found in water sourced environments.
submersible pump connection diagram
A noteworthy aspect to consider during installation, often overlooked, is the pump’s grounding. Proper grounding ensures that any electrical fault that might occur is safely channeled away, significantly reducing risks of electric shock or system damage. Grounding should be executed precisely according to both local electrical codes and manufacturer instructions, commonly involving a dedicated ground wire connected to an earthing rod or integrated into building structure grounding systems.
Submersible pump diagrams also include details about the discharge piping, which should be constructed from suitable materials such as stainless steel or high-density polyethylene (HDPE) to withstand wear and corrosion. The diameter of the discharge piping is crucial, as it impacts the flow rate and efficiency of the pump. The correct diameter allows for optimal water movement, reducing strain on the pump and ensuring that energy consumption remains within desired limits.
For higher expertise engagements, professionals suggest periodic inspections of the system, verifying connections and inspecting components for wear or potential faults. Additionally, utilizing surge protection devices in the electrical system can safeguard against transient voltage spikes induced by lightning or other external factors, enhancing the system’s reliability.
Despite the inherent complexities, assembling an effective submersible pump system is paramount for seamless operation in many water management tasks. Ensuring that each component within the connection diagram is matched according to the technical specifications not only prolongs the life of the equipment but also ensures operational safety and efficiency - factors considered fundamental when designing or maintaining such systems.
For experts in the field, the continuous evolution of pump technology and connectivity innovations represents an exciting frontier. Thanks to smart technology and IoT, modern submersible systems are increasingly capable of sophisticated integration, offering unprecedented control, monitoring capabilities, and heightened reliability. To remain authoritative in the realm of pump systems, professionals must remain informed about these advancements to offer solutions that reflect contemporary technological standards and best practices.