Submersible pumps, renowned for their efficiency and reliability, are an invaluable tool in a wide array of applications ranging from domestic to industrial uses. As an experienced technician, I've had the opportunity to witness and be part of countless submersible pump installations – experiences that have armed me with invaluable insights and reinforced the importance of precision and expertise in their installation process.
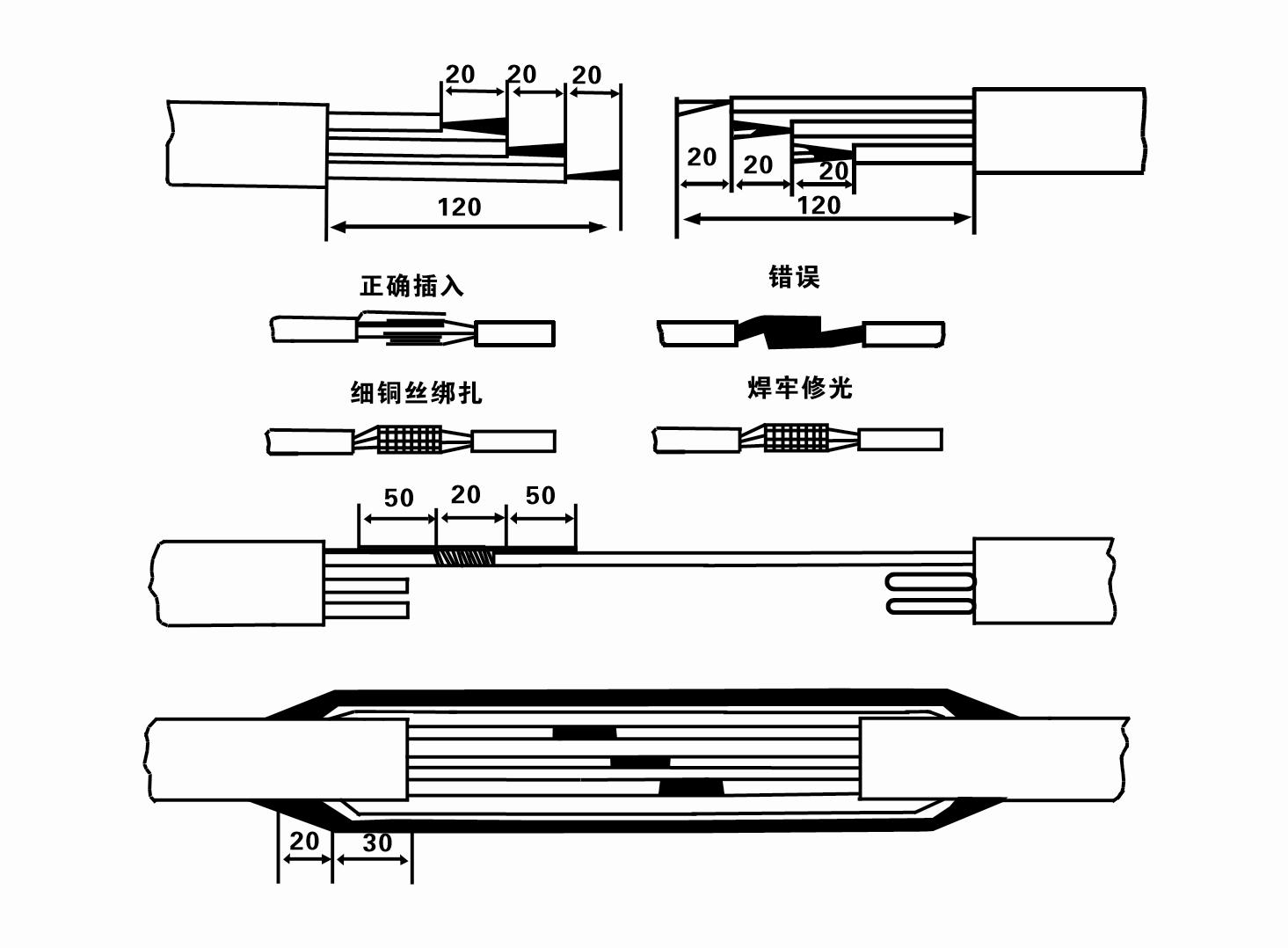
First and foremost,
choosing the right submersible pump is crucial. This decision should be informed by the intended application's specific requirements. Key factors include the fluid type, pumping capacity, and the head – the vertical distance that the pump needs to move the liquid. Opting for a pump that matches these parameters not only ensures optimal performance but also extends the lifespan of the device by preventing issues such as cavitation and overheating.
Preparing the site for installation is the next critical step. Whether the pump is to be installed in a residential well or an industrial sump pit, thorough site preparation is non-negotiable. This includes clearing any debris and ensuring the installation area is clean and easily accessible. During my years of experience, I've observed that improper site preparation often leads to unanticipated problems post-installation, impacting the pump's performance and sometimes causing premature failure.
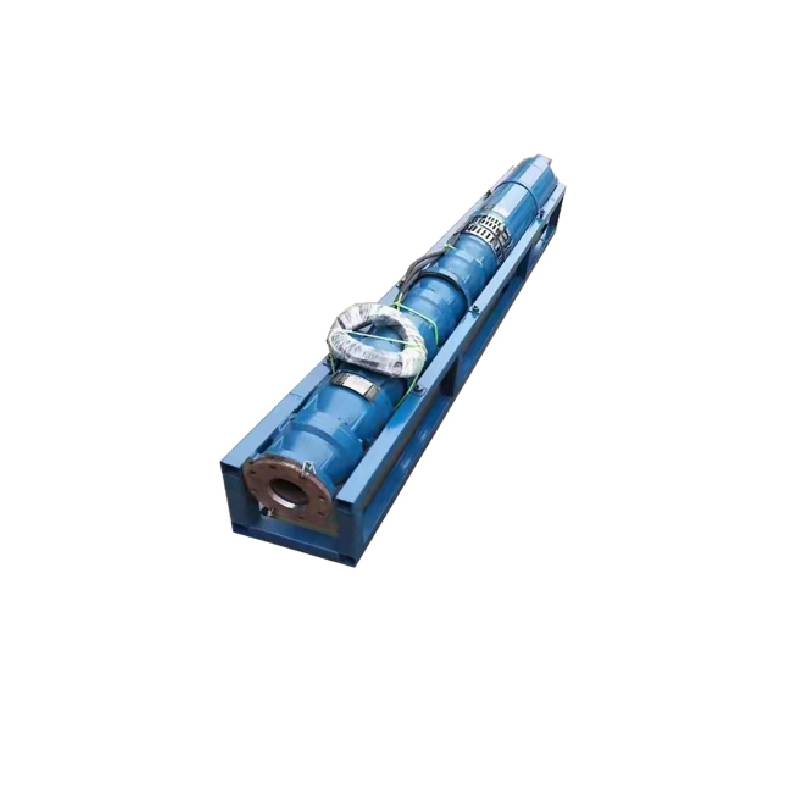
The actual installation of the submersible pump entails several meticulous steps. The pump should be carefully lowered into position using an adequate rope or cable to avoid any physical damage. It is imperative to ensure that all electrical connections are correctly and securely done to prevent hazards such as electrical shorts or inefficiencies in power supply. Moreover, ensuring the installation complies with local electrical codes can safeguard against future regulatory issues and enhance safety.
submersible pump installation
One of the foundational principles of submersible pump installation is ensuring proper sizing and placement of the discharge pipe. The discharge pipe must be adequately sized to handle the pump's flow rate while minimizing friction losses. An often-overlooked aspect is the inclusion of a check valve in the discharge line, which is vital to prevent backflow and water hammer – phenomena that can cause significant damage to the pump and piping system if unchecked.
Equally important is the regular maintenance post-installation, which can significantly influence the pump’s longevity and reliability. Periodic inspection for wear and tear, especially on moving parts and electrical components, is a practice that I cannot overstate. Lubricating components that require it and replacing any damaged parts promptly can prevent small issues from escalating into major ones. This proactive approach is a testament to the pump owner’s commitment to preserving the investment and functional reliability of the equipment.
Modern advances in technology have introduced smart control systems that enhance the functionality and monitoring of submersible pumps. Integrating such systems during installation can provide real-time data and alerts on the pump's performance, enabling swift action against potential problems. My professional experience has shown that when clients incorporate these smart technologies, they not only face fewer emergencies but also benefit from optimized energy consumption, thereby reducing operational costs.
In conclusion, while installing a submersible pump might seem straightforward, the expertise involved is significant. Every stage from the choice of pump to installation, and maintenance commands a precise understanding of both the mechanics and environmental factors. By meticulously following best practices and leveraging technology, one can ensure the submersible pump functions efficiently and has an extended service life. Trustworthiness in the installation process, backed by expertise, underpins the operational success and reliability of the submersible pump system.