Submersible pumps are indispensable tools in various industries, playing a vital role in operations from agriculture to mining. They stand out due to their ability to operate while completely submerged in water or other fluids, which eliminates the need for priming and significantly enhances efficiency.
The efficiency of submersible pumps, however, relies heavily on the integrity of their parts. Understanding these components can lead to better maintenance, longevity, and performance of the pump systems.
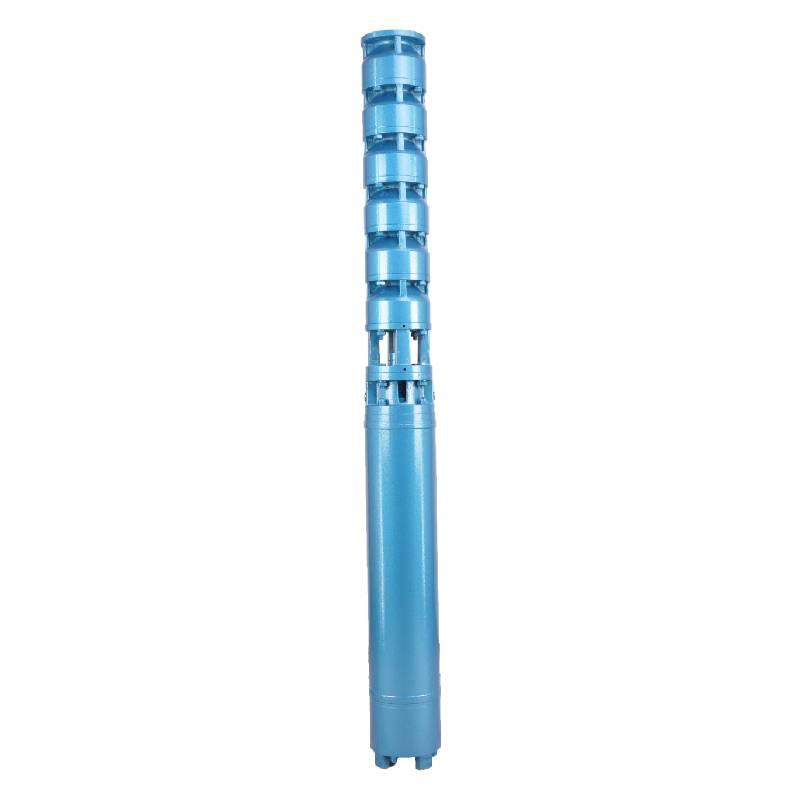
One of the critical components is the impeller, which significantly influences the flow and pressure of the liquid being pumped. Impellers are typically made of durable materials like stainless steel, cast iron, or thermoplastic, to withstand harsh environments. They come in different designs—such as closed, open, or semi-open—each suitable for specific tasks or fluid types. A closed impeller, for example, offers high efficiency for clear fluids, whereas a semi-open impeller provides a better solution for fluids with suspended solids.
Equally important is the shaft, which transfers the rotational energy from the motor to the impeller. Crafted for strength, shafts require materials that resist corrosion and mechanical stress, common choices being stainless steel and carbon steel. Regular inspections of the shaft for alignment and wear can prevent unexpected failures.
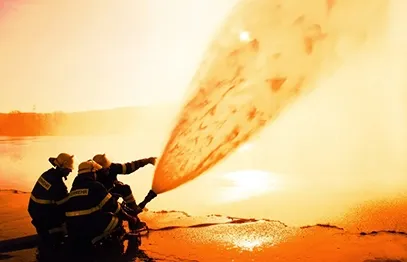
The seal system in a submersible pump is crucial for preventing fluid from entering the motor unit and causing a burnout. Typically, double mechanical seals are used, sitting within the pump's oil chamber to ensure they remain lubricated and effective. The choice and condition of seals can dramatically impact the pump's lifespan and operational reliability, highlighting the necessity of regular checks and replacements.
Another vital component is the motor. Submersible pump motors are usually sealed in oil and designed to operate underwater without overheating. The efficiency of these motors often hinges on the cooling system—a feature that can extend the motor's life through effective heat dissipation. It’s essential to monitor temperature and fluid levels regularly, ensuring that the motor is adequately cooled and lubricated.
submersible pump parts
The pump casing or housing serves as the protective shell for the internal components. Made from robust materials such as cast iron or corrosion-resistant alloys, the casing defends against external elements while maintaining internal pressure levels. Assessing the casing for scratches, dents, or corrosion can prevent minor issues from becoming larger problems.
Finally, the power cable facilitates the supply of electricity to the pump in submerged conditions. These cables are uniquely designed to resist water ingress and maintain their integrity under constant pressure and motion. Regular inspection for wear and potential breaks in the cable insulation can safeguard against electrical failures.
In maintaining submersible pumps, it's essential to consider the integrated nature of its parts. A failure in one area, such as the seal or impeller, can have a domino effect on the entire system. Therefore, routine maintenance and attention to component quality are paramount. Enhanced expertise in understanding these components not only aids in preventing pump downtime but also increases the equipment's reliability and efficiency—key factors in operations that depend on uninterrupted fluid transfer.
Choosing high-quality parts from reputable manufacturers can significantly impact the longevity and performance of your submersible pump. Collaborate with trusted suppliers and prioritize regular maintenance checks as a best practice to ensure that submersible pumps operate at their peak condition, ultimately saving time and resources in the long run.