Priming a submersible pump is an essential procedure that enhances its efficiency and longevity. It ensures that the pump operates smoothly, without any airlocks, and maintains optimal water flow. Drawing on years of expertise and a wealth of real-world experience, this comprehensive guide provides a detailed step-by-step process to prime your submersible pump effectively.
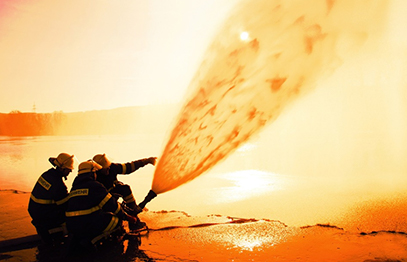
To begin,
it's vital to understand the intrinsic nature of submersible pumps. Their design allows them to function underwater, operating quietly and reliably. However, despite their robust construction and ability to work underwater, they are not immune to airlocks, which occur when air prevents water from flowing through the system. This is where priming comes in.
Start by ensuring that the pump is clean and free from any debris. This pre-emptive step is crucial for maintaining the pump’s longevity and operational efficiency. Before submerging it, inspect the inlet and outlet valves, ensuring they are clear. Any blockage at these points can potentially cause the pump to overheat or fail prematurely.
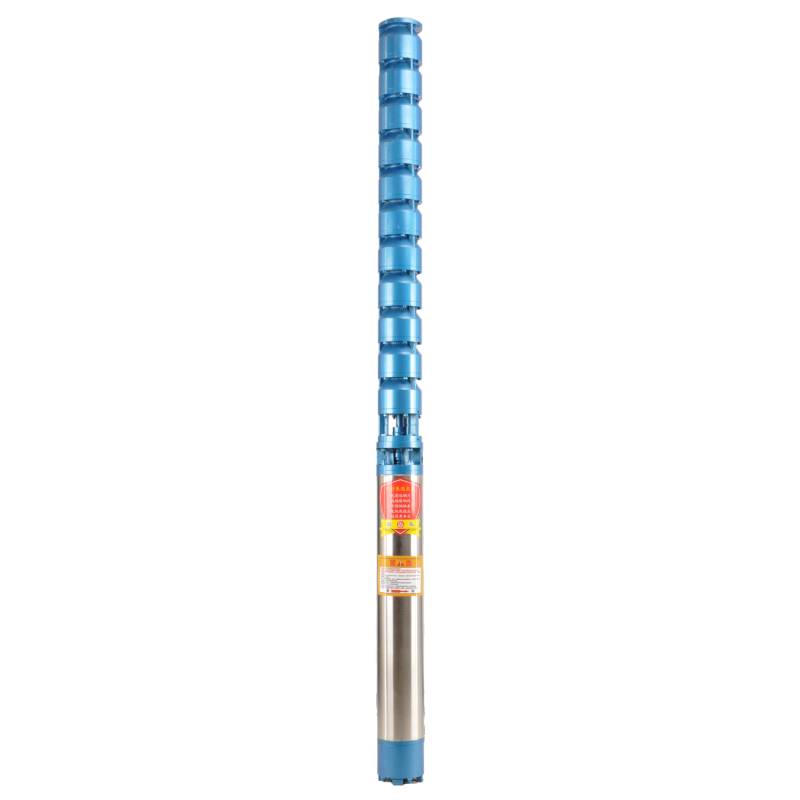
Next, immerse the pump in a container of clean water before placing it in its ultimate location. Doing so will allow you to test the pump’s mechanisms in a controlled environment. While there, make sure that the pump is entirely submerged, eliminating all chances of air being trapped within. This action addresses one of the main causes of airlocks, directly enhancing the pump's performance.
Following this initial immersion, observe the pump’s operation. The water should flow steadily and continuously, signaling that the pump is primed correctly. Any sputtering or interruptions in the flow indicate possible air presence, requiring additional attention. Adjust the submersion depth or reposition the pump slightly, ensuring no air pockets remain trapped inside.
how to prime a submersible pump
For specific applications that demand advanced techniques, consider the use of a priming chamber or vacuum pumps. This step is often necessary when dealing with larger or industrial submersible pumps. The priming chamber fills with water, creating pressure that removes all air. Simultaneously, vacuum pumps extract any residual air, guaranteeing optimal efficiency from the start.
Additionally, for installations involving lengthy pipelines or unique layouts, incorporate one-way check valves. These valves prevent backflow, maintaining all lines filled and ready for operation without re-priming every cycle. Such measures are particularly beneficial in preventing unexpected shutdowns and maintaining system reliability.
Moreover, frequent maintenance cannot be overemphasized. Regular checks, cleaning of components, and inspection for wear are indispensable tasks. By incorporating these routine practices, one develops a habit of monitoring pump efficiency, allowing for proactive troubleshooting and reduced downtime. A keen eye on these procedures fosters trustworthiness, ensuring the pump is always primed and ready for action.
Finally, leveraging expert advice and staying updated with manufacturer guidelines ensures that your priming process aligns with the latest technological insights. Recognizing the value of expert recommendations and real-user testimonials can significantly contribute to optimizing your priming process, thus safeguarding your investment.
By appreciating and applying these versatile strategies, you ensure your submersible pump operates at its best, with maximum efficiency and minimal interruptions. Your mastery of this priming process reflects a deep understanding of the principles involved, boosting your reputation in maintaining and improving water system performances.